Tarkkuusmetalliosat valmistetaan usein erilaisilla tarkkuustyöstötekniikoilla, joista CNC-työstö on yleinen menetelmä. Tarkkuusosille asetetaan yleensä korkeat vaatimukset sekä mitoille että ulkonäölle.
Siksi CNC-työstettäessä metalleja, kuten alumiinia ja kuparia, työkalun jälkien ja viivojen esiintyminen valmiin tuotteen pinnalla on huolenaihe. Tässä artikkelissa käsitellään syitä, jotka aiheuttavat työkalun jälkiä ja viivoja metallituotteiden koneistuksen aikana. Ehdotamme myös mahdollisia ratkaisuja.
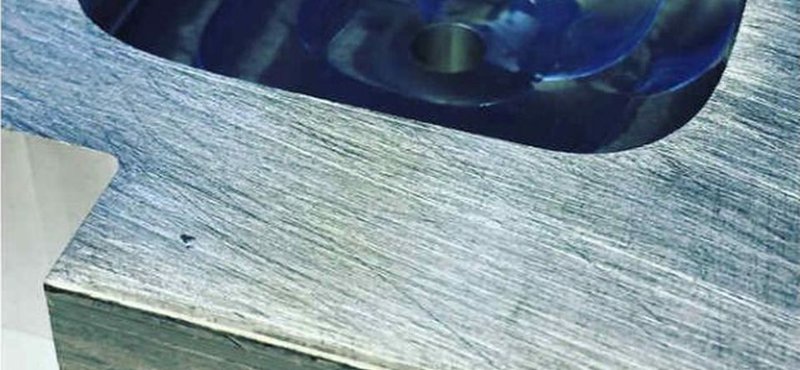
Kiinnityslaitteiden riittämätön puristusvoima
Syyt:Joissakin ontelometallituotteissa on käytettävä alipainelaitteita, ja niillä voi olla vaikeuksia tuottaa riittävää imua pinnan epätasaisuuksien vuoksi, mikä johtaa työkalun jälkiin tai viivoihin.
Ratkaisu:Tämän lieventämiseksi harkitse siirtymistä yksinkertaisesta alipaineimurista alipaineimuriin yhdistettynä paineeseen tai sivuttaistukeen. Vaihtoehtoisesti voit tutkia vaihtoehtoisia kiinnitysvaihtoehtoja tiettyjen osarakenteiden perusteella ja räätälöidä ratkaisun kyseiseen ongelmaan.
Prosessiin liittyvät tekijät
Syyt:Tietyt tuotteiden valmistusprosessit voivat osaltaan vaikuttaa ongelmaan. Esimerkiksi tablet-tietokoneiden takakuoret käyvät läpi sarjan koneistusvaiheita, joihin kuuluu sivureikien lävistäminen ja reunojen CNC-jyrsintä. Tämä prosessi voi johtaa havaittaviin työkalun jälkiin, kun jyrsintä saavuttaa sivureikien sijainnit.
Ratkaisu:Yleinen esimerkki tästä ongelmasta ilmenee, kun alumiiniseos valitaan elektroniikkatuotteiden kuoriin. Ongelman ratkaisemiseksi prosessia voidaan muokata korvaamalla sivureikien lävistys ja jyrsintä pelkällä CNC-jyrsinnällä. Samalla varmistetaan tasainen työkalun kiinnitys ja vähennetään epätasaista leikkausta jyrsinnän aikana.
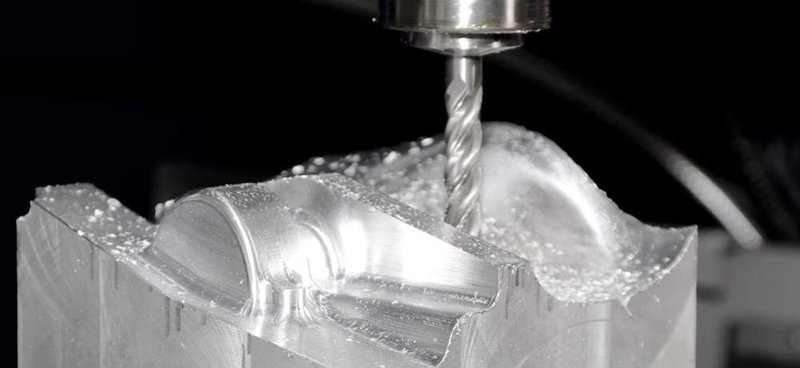
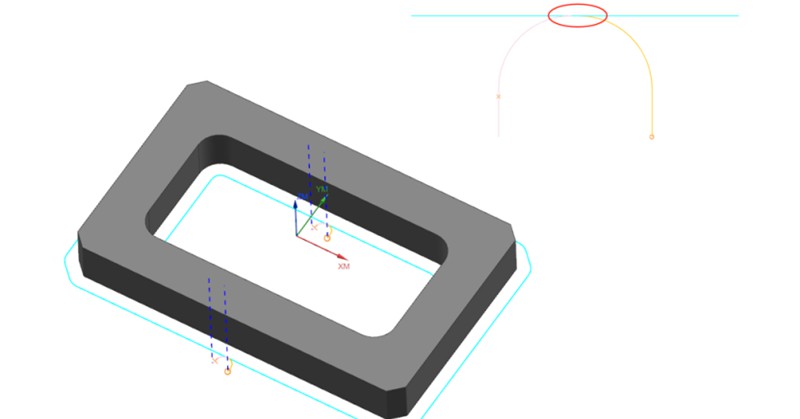
Työkalun radan kytkeytymisen riittämätön ohjelmointi
Syyt:Tämä ongelma ilmenee yleisesti tuotetuotannon 2D-profiilin koneistusvaiheessa. Huonosti suunniteltu työkalun radan kytkentä CNC-ohjelmassa jättää jälkiä työkalun sisään- ja ulostulopisteisiin.
Ratkaisu:Työkalun jälkien välttämisen haasteeseen sisään- ja ulostulokohdissa vastataan tyypillisellä lähestymistavalla, jossa työkalun kosketusetäisyydessä on pieni päällekkäisyys (noin 0,2 mm). Tällä tekniikalla vältetään mahdolliset epätarkkuudet koneen johtoruuvin tarkkuudessa.
Vaikka tämä strategia estää tehokkaasti työkalun jälkien muodostumisen, se aiheuttaa toistuvaa työstöä, kun tuotteen materiaali on pehmeää metallia. Tämän seurauksena tässä osassa voi olla eroja rakenteessa ja värissä verrattuna muihin alueisiin.
Kalan suomukuviot tasaisilla koneistetuilla pinnoilla
Syyt:Tuotteen tasaisilla pinnoilla esiintyy kalansuomuja tai pyöreitä kuvioita. Pehmeiden metallien, kuten alumiinin/kuparin, työstämiseen käytettävät leikkaustyökalut ovat yleensä metalliseosten jyrsimiä, joissa on 3–4 uraa. Niiden kovuus vaihtelee HRC55:stä HRC65:een. Nämä jyrsintätyökalut työstetään työkalun alareunaa käyttäen, ja osan pintaan voi muodostua tunnusomaisia kalansuomuja, jotka vaikuttavat sen yleisilmeeseen.
Ratkaisu:Yleisesti havaittavissa tuotteissa, joilla on korkeat tasaisuusvaatimukset ja upotetut rakenteet omaavilla tasaisilla pinnoilla. Korjauskeinona on siirtyä synteettisestä timantista valmistettuihin leikkaustyökaluihin, jotka auttavat saavuttamaan tasaisemmat pinnanlaadut.
Laitteiden osien ikääntyminen ja kuluminen
Syyt:Työkalun jäljet tuotteen pinnalla johtuvat laitteen karan, laakereiden ja johtoruuvin ikääntymisestä ja kulumisesta. Lisäksi riittämättömät CNC-järjestelmän välysparametrit vaikuttavat voimakkaisiin työkalun jälkiin, erityisesti pyöristettyjä kulmia työstettäessä.
Ratkaisu:Nämä ongelmat johtuvat laitteisiin liittyvistä tekijöistä, ja niihin voidaan puuttua kohdennetulla huollolla ja vaihdolla.
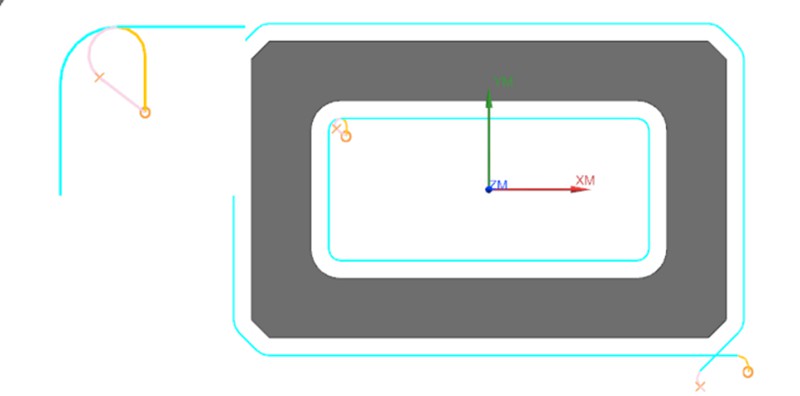
Johtopäätös
Ihanteellisen pinnan saavuttaminen CNC-työstetyissä metalleissa vaatii hyödyllisiä lähestymistapoja. Työkalujälkien ja -viivojen välttämiseksi on olemassa erilaisia menetelmiä, joihin liittyy laitteiden huoltoa, kiinnittimien parannuksia, prosessin säätöjä ja ohjelmoinnin hienosäätöä. Ymmärtämällä ja korjaamalla nämä tekijät valmistajat voivat varmistaa, että tarkkuuskomponentit eivät ainoastaan täytä mittavaatimuksia, vaan myös niillä on halutut esteettiset ominaisuudet.